What is a prototype?
If you have an ambitious idea, don’t jump into production! First, create a prototype – it’s like making a trial run of your product to put it through its paces. It helps test the viability of your concept and can improve accuracy by getting feedback from system analysts and users.
Prototypes come in many shapes and sizes (e.g., semantics, design, electronics), so whatever type of project you’re working on, there’s sure to be one that suits your needs!
Prototyping enables the development of a functional system based on defined requirements instead of a theoretical one.
Paper drawings may be the most basic form of a product prototype. However, digital prototypes can also offer invaluable insights.
Digital prototypes are useful for refining the design, materializing your product idea, and providing a platform for feedback from engineers and other stakeholders.
Following these steps, of course, you can make physical prototypes as well.
Draw or create a through diagram
Step one in prototyping is to get that idea out of your head and onto paper! Start sketching like a storm and capture as many creative thoughts as possible. When you’re done, lay back and pat yourself on the back for creating something incredible!
There should be two idea sketches:
- A design drawing illustrates what the finished product will look like.
- The technical drawing should include dimensions, materials used, and its various functional components.
You have limitless opportunities for creativity when designing a prototype!
Explore the potential of various software programs while taking advantage of the timeless pen-and-paper approach – allowing you opportunities to be creative.
Take some risks during this exploration phase, as there’s still plenty of room in the journey from concept to production.
Ready to enter the 3rd dimension?
Make a 3D model
Now it’s time to take your concept to the next level by importing it into a 3D modeling program. It will give you an accurate visual of your product’s appearance in real life and make changes as needed.
Plus, you’ll also be able to use this model to create a 3D-printed prototype which is an awesome bonus!
Make a concept proof
The construction of your first proof of concept hinges on various factors. If you have already simulated a specific product on 3D software, it can be effortlessly brought to life by having it 3D printed for testing.
You must put in more effort to improve if you have a complex product with multiple mechanical and electrical components.
Build your first prototype
Your proof of concept shows the functionality of your product, while your 3D model provides a visual representation of its potential design.
Now it’s time to mix the amazing stuff you’ve learned about your proof of concept and 3D modeling into one awesome prototype!
This model should be highly detailed and closely resemble the eventual outcome of your product.
Depending on the complexity, developing a detailed initial prototype on your own can be difficult. To ensure success, seeking help from a qualified machinist or prototype designer may be beneficial.
Make a production-ready prototype
The final step before manufacturing is to refine the prototype and ensure it is ready for production. It may involve facilitating the design to eliminate unnecessary elements.
Undertaking a cost-benefit analysis is an essential step in prototype development. To ensure the most effective solution is achieved, carefully consider each component, and identify potential ways to reduce expenditure without compromising function or performance.
At the same time, aim to boost that product – extra good looks and lasting strength!
Replace commonly used plastic parts with metal and infrequently used metal components with plastic to help reduce costs without compromising quality.
Working closely with a manufacturer to evaluate the cost and quality impacts of different components in a prototype can be beneficial. Furthermore, exploring various raw materials to ascertain which ones will offer an optimal aesthetic appeal is prudent.
Your goal should be to strike the right balance between price and quality, depending on your target customers. For instance, if you aim at premium buyers, quality should take priority over cost; however, for those with lower incomes, the reverse may be true.
Types of prototypes
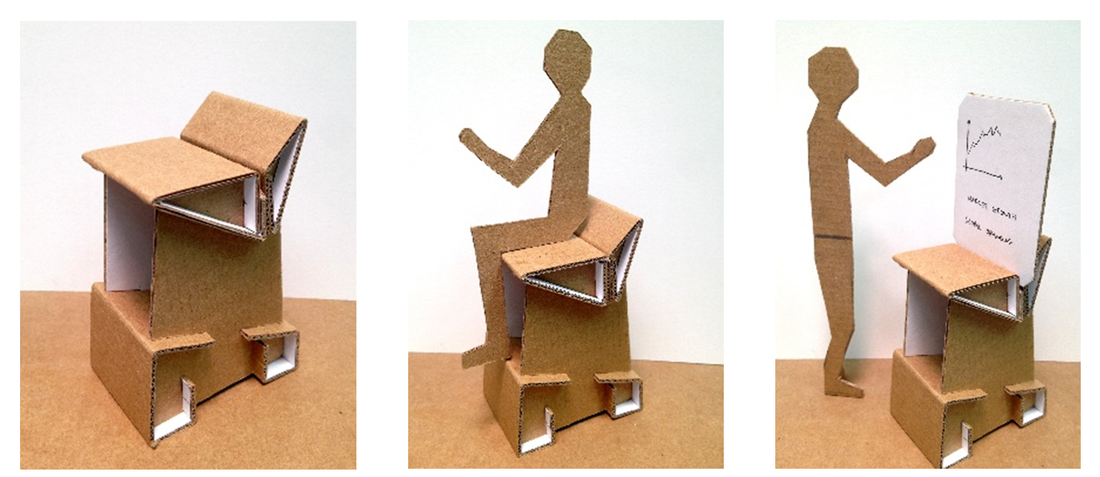
Feasibility prototypes
It’s used to test technical limitations.
- To test new technology prototypes
- The engineer develops just enough code to determine feasibility.
- It helps understand technical risk, which is often tied to performance.
Low-fidelity user prototypes
It evaluates the value of proposed solutions.
- Essentially an interactive wireframe
- Interactive designers create this to test the process
- Simulates the process of identifying usability concerns early on
High-fidelity user prototypes
It evaluates user experience.
- Working simulation with a realistic look
- Excellent for informing stakeholders about a proposed product
- Utilize defensive user testing to determine whether users will find the product acceptable.
Live data prototype
It is a behavior assessment.
- Developers construct a very minimal version to verify it works
- This technology provides instant access to real-time data and delivers timely traffic updates.
- It has yet to be developed into a commercialized product. (no test automation, SEO, localization, etc.)
What are the benefits?
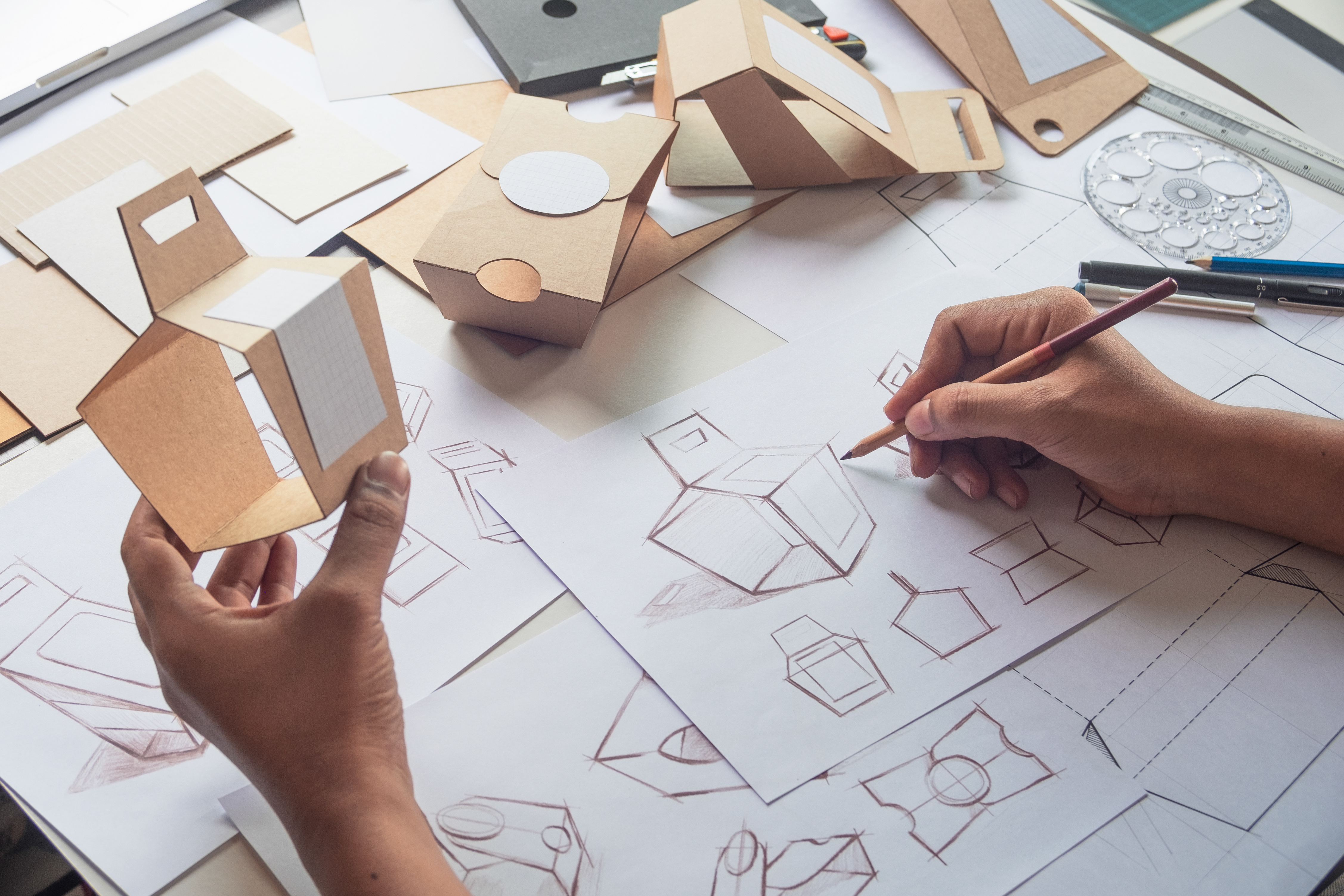
Reduce risk
Beginning your journey with early prototyping can help you minimize potential risks. Prototyping quickly will enable you to identify any issues or flaws that could be present and provide you with an in-depth understanding of what your customers want and their thoughts on the product concept. This research will allow the crafting of a product capable of meeting the needs of its users and standing out among similar products available in the market.
Test ideas
Prototypes can be a great way of quickly testing out feature ideas. Even with something as simple as a paper prototype, you can get an idea of how users and your team may respond within no time. The utility of design tools is invaluable throughout product development, providing significant support for informed decision-making.
Refining product design
Prototyping offers a considerable advantage in that it allows for the refinement of the final product design. An interactive, three-dimensional product version will enable flaws or potential issues to be easily identified and rectified before production.
Test materials
A sketch or computer model serves as a blueprint, allowing you to turn the virtual world into reality. It provides an opportunity to experiment with how various materials look, perform, and interact with each other to find the best combinations possible.
Test environmental conditions
Ensuring your product’s performance can be achieved by conducting various tests in varying environmental conditions. This way, you can reduce the possibility of customers encountering issues like shorting out and breakages after just a few uses, as seen with many cheaper electronic goods.
Test manufacturing processes
Prototyping is an important step to ensure the success of a product. Not only does it allow for testing, it also provides the opportunity to verify and refine manufacturing methods that can yield a higher quality product and make transitioning into production much smoother.
Improve user safety and regulatory compliance
Prototyping is essential for guaranteeing not only the safety of your product but also its optimal performance. It allows you to identify potential issues quickly and helps you to attach to industry regulations, ensuring a much higher level of user protection.
Spend less money
Any modifications to product design, materials, or manufacturing processes made during the prototype phase could help reduce costs associated with producing the final product. It also reduces potential risks such as legal and financial consequences due to a major fault or a recall of the last made item.
Stakeholders can see the final product
Creating a physical prototype that stakeholders can view, modify and evaluate helps speed up the design process. It includes decision-makers, customers, investors, and other important audiences.
First steps with prototyping
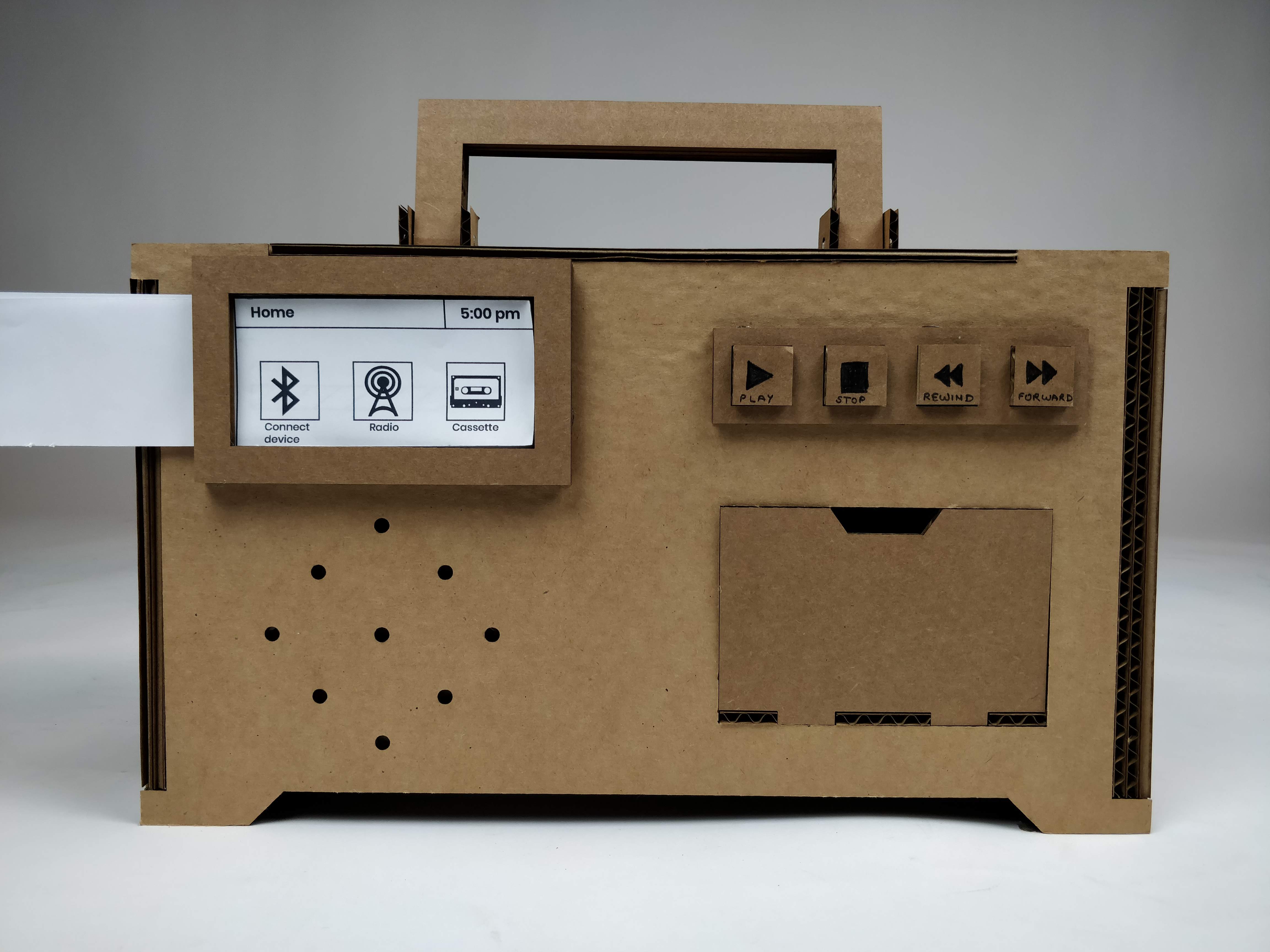
Before drawing your actual prototype, thoroughly researching the business concept is important. Investigate the market, analyze competitors, and assess customer needs to understand the landscape better.
It will enable you to concentrate on certain market segments and create a more effective prototype.
Here are some questions you should ask yourself:
What problem will the product solve?
Take the time to evaluate how your product can benefit its users. Analyze the needs of your target audience and develop a strategy that meets them effectively to achieve a successful solution.
If you want to get the big picture of your product, break it down into its basic parts and write a problem statement – the perfect way to piece together your invention!
What similar products are currently on the market?
Explore opportunities beyond your current field to identify similar products already in use and gather user feedback. Consider a wide range of industries rather than limiting yourself to only one.
You may find a solution to the same problem tailored to a different audience.
Who is your target user?
Understand your target audience, what they desire and need from your product, and how it will be used. Think objectively – remove personal expectations to consider the user’s perspective. Embrace creative solutions beyond the traditional approach to gain new insights into the product’s potential uses.
What kind of product is it?
Think about your audience and their goals–it’s like designing the perfect product! And it all starts with picking the right device for them–will it be a smartphone or something more?
You could consider platforms to give those devices compatibility across multiple systems. But remember, different age groups will have different usage types; some may use smartphones mostly for playing games.
So, you must know what kind of product you’ll make before building that prototype!
What are the prototyping process goals?
Before you get prototyping, set some goals! What do you want it to do?
Will a scaled-down version work, or will your prototype need bells and whistles?
Lay out a plan to build the perfect model– with the help of paper or digital technology. Then take off on your journey to creating something wonderful and fulfilling those objectives!
Rapid prototyping
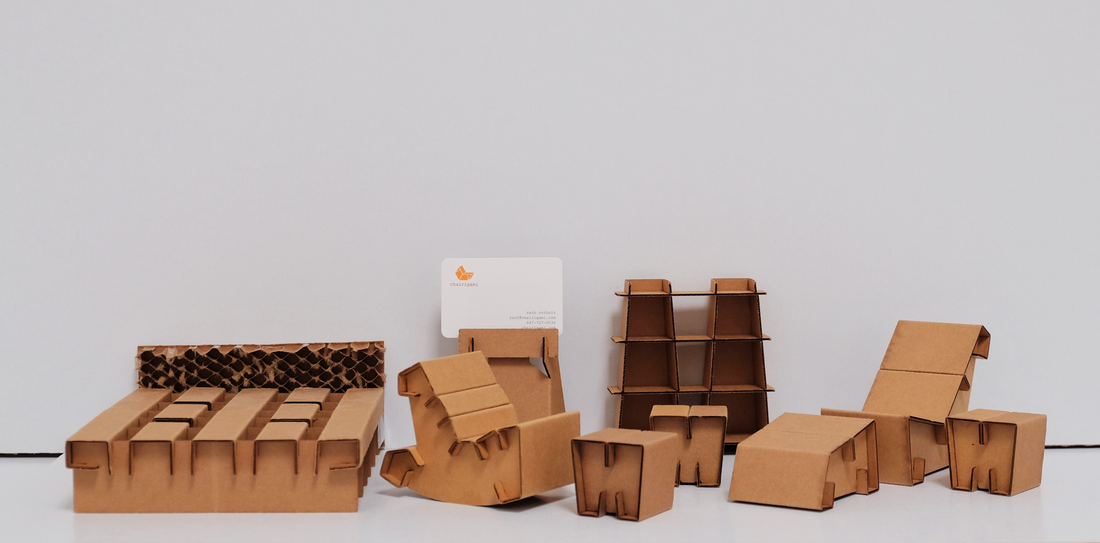
What is rapid prototyping?
Let your ideas come to life and give them shape! With 3D CAD (3D Computer Aided Design) data and rapid prototyping techniques, you can quickly bring your designs into the physical world. From concept to creation, add layer after layer of material with 3D printing or “additive manufacturing” until you have a scale model of the real deal!
Make your product ideas come to life like a lightning bolt!
Rapid prototyping is the key – it puts the power in your hands to check out any part of the process, anytime, from concept to completion.
Your creativity will shine with rapid prototyping, and you’ll always have perfect components.
Rapid prototyping is an innovative concept that allows for the fast production of prototypes to assess their appearance and function quickly.
Using quick manufacturing processes, individual components can be assembled on time to check how the prototype performs.
Why rapid prototyping is important?
Companies must stay competitive in today’s fast-paced consumer market by quickly creating and releasing new products.
Rapid prototyping is essential for successful product development, as the speed of production and technological advances are integral to a company’s success.
Rapid prototyping achieves the following goals.
- Rapid prototyping is essential for achieving a successful product outcome in quickly developed products, as it drastically speeds up the product development process.
- It verifies the feasibility of the design’s form, fit, and purpose in its initial stages.
- Validate the final product against technical requirements and business objectives to ensure they are met.
- It allows for functional testing to ensure the concept’s objectives are met and complete the product design.
Advantages of rapid prototyping
- Speed up the design and manufacturing process
- Reduce or eliminates the risk
- Ability to assess human factors and ergonomics
- Reduce the product development process
- Allows for low-cost functionality testing.
- Improved and expanded involvement by users
Disadvantages of rapid prototyping
- Increased initial cost – Rapid prototyping is expensive due to the technology employed and the faster turnaround period required.
- Some rapid prototyping procedures still need to be more expensive and efficient.
- Reduced material attributes such as surface finish and strength
- Rapid prototyping requires skilled labours
- Limited material range
- Prototyping without certain key features may lead to inaccurate testing results
Ways to make a prototype on a limited budget
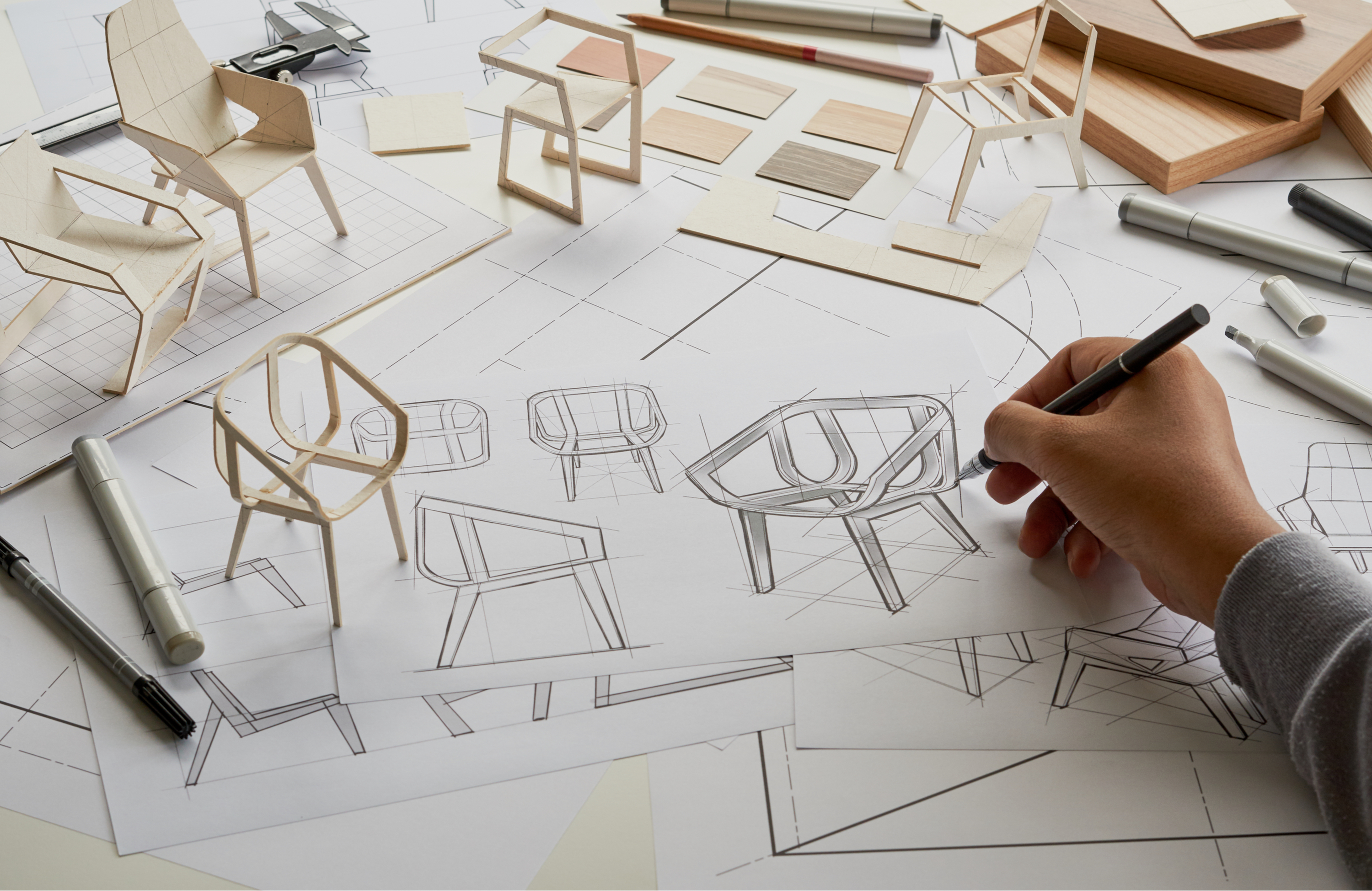
Follow lean startup methodology: The best way to make a prototype on low budget is to follow lean startup methodology.
What is Lean startup methodology?
The Lean Startup methodology provides a feedback loop to help you assess the viability of your company concept.
By building, measuring, and learning, you can quickly identify if there is customer interest in what your business proposes.
Should the results not be as expected, use them to inform any necessary changes or pivots to refine your plans.
Start with hand sketches: Begin by sketching out your idea on paper or utilizing digital tools. This way, you can quickly assess the feasibility of your concept and make necessary adjustments without incurring any expenses.
Use low-cost materials: Do your best and spend less! Keep an eye out for low-cost materials like cardboard or any recyclable material. Use these materials to build your prototype structure – it will reduce the cost.
Use 3D printing: If you’re looking to bring your idea to life without significant financial investment, 3D printing is an excellent solution.
Low-cost 3D printers can now be found on the market, making it simple to get started with prototyping your designs. If you don’t have your printer at home, find a local maker space for cost-effective 3D printing services.
Whatever method you choose will provide an easy and affordable way to create models without spending much money.
Use virtual prototyping: Construct your product prototype effortlessly – use CAD (Computer Aided Design) software to create an awesome virtual version!
With CAD, you can set up the perfect design in no time and start experimenting with new ideas. Plus, you don’t even have to invest in physical components!
Collaborate with others: Connect with other entrepreneurs and like-minded individuals with the necessary skills or experience to assist you in prototype development.
Exchanging resources and advice can help you improve your prototypes more efficiently while reducing costs.
Crowdfunding platforms: Explore the possibility of using crowdfunding platforms to finance the production of your prototype. Put forth a compelling presentation outlining your idea and provide early bird discounts for supporters to incentivize participation. Gather support from individuals who believe in you and your project!
Use DIY electronics: If you want to add electronics to your prototype, a DIY approach can be cost-effective. Instead of breaking the bank on specialized components, you can save money and still build a fully functional prototype using readily available Do-It-Yourself electronics products!
Test your prototype
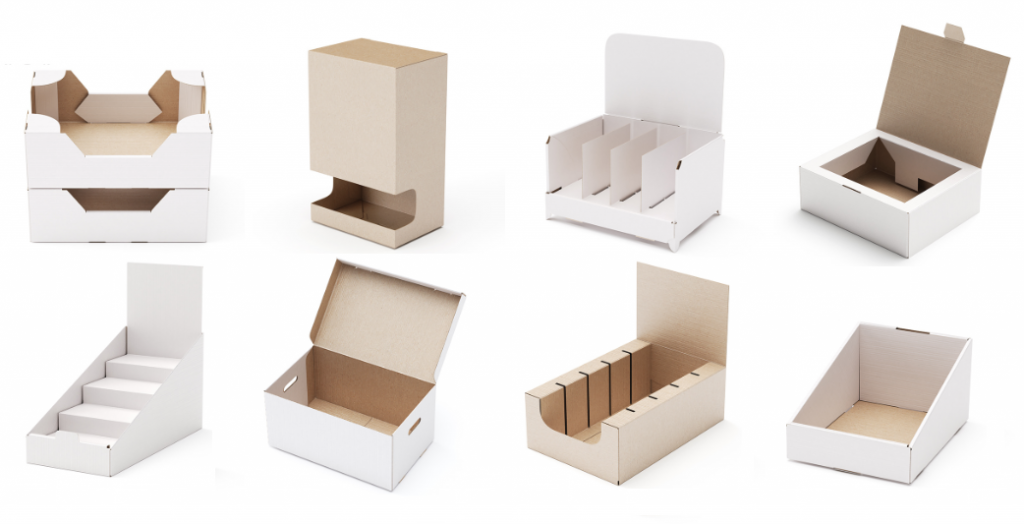
Now that the prototype is completed, it’s time to start testing. For testing the prototype, numerous approaches can be taken. To ensure that desired results are obtained, base your testing method on your expected outcome.
What are the advantages of testing a prototype?
Prototype testing has many benefits, making it a desirable step in product release. By utilizing this stage, you can be assured that the design has been proven through user feedback before releasing it to the market. Additionally, major usability issues can be identified and remedied earlier in the design cycle.
Let’s look at some of the best reasons to test prototypes.
Find issues in your design
You need to test your prototype before launching a product on the market to avoid poor performance resulting in a failed product. Through testing, you will be able to identify any issues with the design and improve them before releasing them to consumers. It helps ensure success by avoiding costly mistakes from being released to the public.
Gather valuable customer feedback early
Make sure to get feedback from real people first!
Taking the time to receive customer input can help you avoid any negative user experiences down the line, thus preventing bad reviews and unhappy customers.
Time and cost savings
Identifying and resolving design flaws, usability issues, or functional limitations in the early development stage can significantly reduce time and money costs. Finding potential problems during the prototype phase allows for preventive measures to be taken, thus avoiding expensive alterations or reconsiderations when already deep into other stages of production.
Cut the risk
Testing a prototype can minimize unpredictability and equip your team with the data to make informed decisions in the subsequent development stages. It allows for early identification and reduction of risks, such as technical feasibility, market acceptance, usability challenges, or potential regulatory difficulties. By addressing these issues during the prototyping phase, you can ensure smooth progress throughout each step in your product’s lifecycle.
Market validation
Testing a prototype with potential users or customers can give you invaluable insights into the viability of your product concept in the market. You can gain an understanding of user interests, preferences, and needs to determine whether there is sufficient scope for success. This information can guide you in developing a go-to-market strategy that gives your product the best chance of success.
Confidence building
Prototype testing can give you the assurance you need for your product’s success. By collecting user feedback, witnessing satisfaction, and addressing any problems that may arise, you can be confident in your product’s viability and overall effectiveness as it progresses through development.
Pain points in prototyping
Unfortunately, no product development model is without its drawbacks. Creating a prototype has several downsides that should be considered.
Let’s see what is common in it.
Time consuming
Developing a functioning prototype can be an incredibly time-consuming process. Multiple prototypes are typically created to test the product before the final release thoroughly, so the development cycle can take as much time as it does.
Ineffective decision-making
The developer is always mindful of ensuring high-quality output with their product. However, the timeline to complete the prototype may cause them to make decisions that could compromise its overall quality and harm the final product.
High upfront cost
Developing a prototype model can offer considerable cost savings during the latter stages of development. However, several upfront costs may be associated with creating a prototype early in the process. Moreover, these expenditures could be for nothing if the entire model needs to be discarded.